Heraenium® Pw
Overview
Specifications
Specification legend
Downloads
Cobalt-chrome-based bonding alloy for conventional ceramics especially for HeraCeram acc. to EN ISO 9693-1 and 22674
Product details | ||||||||||||||
---|---|---|---|---|---|---|---|---|---|---|---|---|---|---|
Composition (content in mass %) |
Co 55.2 Cr 24.0 Mn 0.8 Si 1.0 N x Fe 4.0 W 15.0 |
|||||||||||||
Type | 5 (k),4 (s) | |||||||||||||
Shade | Grey | |||||||||||||
Indication | 3,4,5,6 | |||||||||||||
Article Code |
Technical data melting and casting | ||||||||||||||
---|---|---|---|---|---|---|---|---|---|---|---|---|---|---|
Melting range |
Solidus 1320 ° C Liquidus 1400 ° C |
|||||||||||||
Preheating temperature | 950 ° C | |||||||||||||
Casting temperature | 1550 ° C | |||||||||||||
Crucible |
Ceramic NPM |
|||||||||||||
Density | 8.9 g/cm3 | |||||||||||||
Hardness (HV5) | 290 HV10 (w/k) 275 HV10 (s) | |||||||||||||
0.2 % yield strength (MPa) | 530 (w/k), | |||||||||||||
Elongation (%) | 8 (w/k) | |||||||||||||
Young's modulus of elasticity (GPa) 100 | 208 |
Ceramic firing | ||||||||||||||
---|---|---|---|---|---|---|---|---|---|---|---|---|---|---|
CTE | 14.3 | |||||||||||||
Oxide firing | 950 °C 3) / 10 min.(vacuum) | |||||||||||||
Soft annealing | --- | |||||||||||||
Hardening | --- |
Solder / Laser welding wire | ||||||||||||||
---|---|---|---|---|---|---|---|---|---|---|---|---|---|---|
Solder |
suitable dental CoCr basic solders according to EN ISO 9333/Stahlgold Lot 750 |
|||||||||||||
Laser welding wires | suitable dental CoCr laser welding wires according to EN ISO 28319 |
Composition:
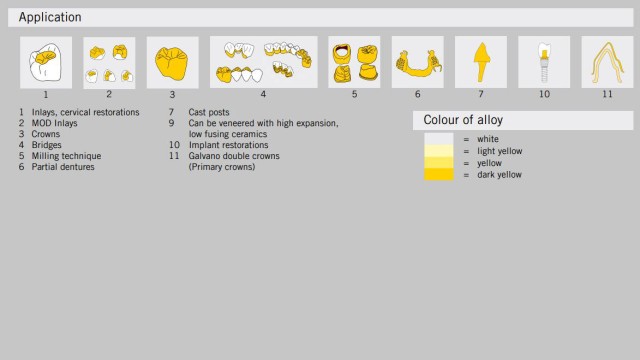
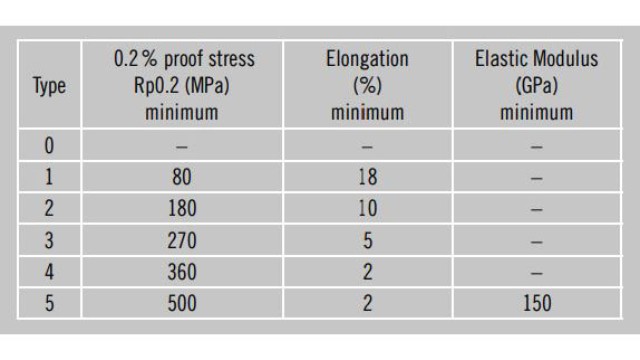
w = After soft annealing and quenching
k = Bonding alloy: condition after ceramic firing
v = Condition after hardening
s = Self-hardening alloy, after slow cooling in the mould
Remarks
A = A stable framework design with reinforced connections with a cross-section of 8 –10 mm2 is required for long span bridges and suprastructures. Additionally, the frameworks need to be hardened.
B = Depending on the copper and/or silver content, in some cases discoloration of double crowns may result after short period of wearing.
C = In exceptional cases these alloys can also be used for traditional telescopic crowns with parallel walls and for the bar casting technique provided that cross-sections for crown walls, approximal areas, bars and laser welded joints are particularly thick and the alloy is hardened subsequently. No indication for conical crowns and shear distributors.
D = Type classification acc. EN ISO 22674
Technical Data, Melting and Casting:
Contraindications
In case of hypersensitivity (allergies) to one of the constituents of the alloy.
Side effects
In individual cases hypersensitivity reactions (allergies) or electrochemically conditioned, local malsensations were reported.
Interactions with other dental alloys
With approximal or antagonist contact with dentures of different alloys galvanic effects may occur. Other materials must be used instead if contact with other alloys causes persistent local paraesthesia on an electrochemical basis.
1) Acc. to EN ISO 22674
2) 1MPa = 1N/mm², 1GPa = 1000 N/mm²
3) When veneered with ceramics, these alloys do not require any additional hardening process to provide their max. physical values.
4) Normally, the pre-heating temperature shall be 900 °C. In case of form filling problems with thin copings we recommend to raise the pre-heating temperature to 950 °C.
5) For cast-on technique
Ceramic Firing:
Remarks
1) When veneering with ceramics with higher firing temperature, oxide firing must be carried out at the highest ceramic firing temperature; max. temperature of 950 °C must not be exceeded.
2) Oxide firing: Please follow the instructions of the ceramic manufacturer.
3) Follow the instructions of the ceramic manufacturer.
4) Hardening prior to firing (conditioning for milling techniques): 930 °C, 15min, rapid cooling.
5) When veneered with ceramics, these alloys do not require any additional hardening process to provide their maximum physical values.
6) 25 – 500 °C acc. EN ISO 9693
Solders / Laser Welding Wires:
Remarks
* The working temperature is part of the solder’s name.
** Recommended flux:
Precious metal/ precious metal: use suitable flux
Precious metal/ non precious metal: use suitable flux
Non precious metal/ non precious metal: use suitable flux
1) Herador Lot V800 must be soldered under vacuum. Graphite firing trays should be used.
2) Recommended alternative alloy.
3) When processed with HeraCeram.
5) Accurate temperature control must be ensured. 740 °C must not be exceeded. Maximum heat-rate: 55 °C/min.
Overview
Cobalt-chrome-based bonding alloy for conventional ceramics especially for HeraCeram acc. to EN ISO 9693-1 and 22674
Specifications
Product details | ||||||||||||||
---|---|---|---|---|---|---|---|---|---|---|---|---|---|---|
Composition (content in mass %) |
Co 55.2 Cr 24.0 Mn 0.8 Si 1.0 N x Fe 4.0 W 15.0 |
|||||||||||||
Type | 5 (k),4 (s) | |||||||||||||
Shade | Grey | |||||||||||||
Indication | 3,4,5,6 | |||||||||||||
Article Code |
Technical data melting and casting | ||||||||||||||
---|---|---|---|---|---|---|---|---|---|---|---|---|---|---|
Melting range |
Solidus 1320 ° C Liquidus 1400 ° C |
|||||||||||||
Preheating temperature | 950 ° C | |||||||||||||
Casting temperature | 1550 ° C | |||||||||||||
Crucible |
Ceramic NPM |
|||||||||||||
Density | 8.9 g/cm3 | |||||||||||||
Hardness (HV5) | 290 HV10 (w/k) 275 HV10 (s) | |||||||||||||
0.2 % yield strength (MPa) | 530 (w/k), | |||||||||||||
Elongation (%) | 8 (w/k) | |||||||||||||
Young's modulus of elasticity (GPa) 100 | 208 |
Ceramic firing | ||||||||||||||
---|---|---|---|---|---|---|---|---|---|---|---|---|---|---|
CTE | 14.3 | |||||||||||||
Oxide firing | 950 °C 3) / 10 min.(vacuum) | |||||||||||||
Soft annealing | --- | |||||||||||||
Hardening | --- |
Solder / Laser welding wire | ||||||||||||||
---|---|---|---|---|---|---|---|---|---|---|---|---|---|---|
Solder |
suitable dental CoCr basic solders according to EN ISO 9333/Stahlgold Lot 750 |
|||||||||||||
Laser welding wires | suitable dental CoCr laser welding wires according to EN ISO 28319 |
Specification legend
Composition:
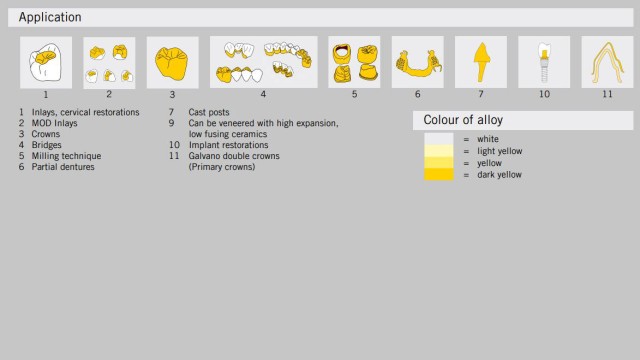
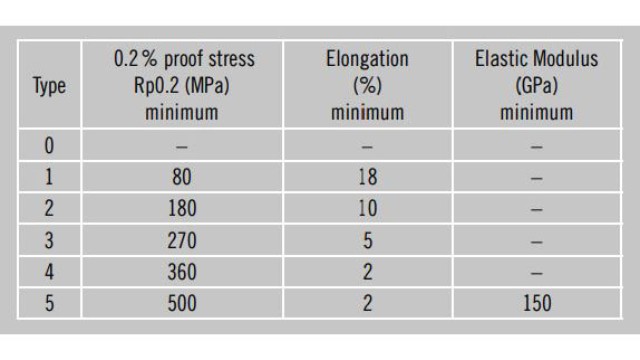
w = After soft annealing and quenching
k = Bonding alloy: condition after ceramic firing
v = Condition after hardening
s = Self-hardening alloy, after slow cooling in the mould
Remarks
A = A stable framework design with reinforced connections with a cross-section of 8 –10 mm2 is required for long span bridges and suprastructures. Additionally, the frameworks need to be hardened.
B = Depending on the copper and/or silver content, in some cases discoloration of double crowns may result after short period of wearing.
C = In exceptional cases these alloys can also be used for traditional telescopic crowns with parallel walls and for the bar casting technique provided that cross-sections for crown walls, approximal areas, bars and laser welded joints are particularly thick and the alloy is hardened subsequently. No indication for conical crowns and shear distributors.
D = Type classification acc. EN ISO 22674
Technical Data, Melting and Casting:
Contraindications
In case of hypersensitivity (allergies) to one of the constituents of the alloy.
Side effects
In individual cases hypersensitivity reactions (allergies) or electrochemically conditioned, local malsensations were reported.
Interactions with other dental alloys
With approximal or antagonist contact with dentures of different alloys galvanic effects may occur. Other materials must be used instead if contact with other alloys causes persistent local paraesthesia on an electrochemical basis.
1) Acc. to EN ISO 22674
2) 1MPa = 1N/mm², 1GPa = 1000 N/mm²
3) When veneered with ceramics, these alloys do not require any additional hardening process to provide their max. physical values.
4) Normally, the pre-heating temperature shall be 900 °C. In case of form filling problems with thin copings we recommend to raise the pre-heating temperature to 950 °C.
5) For cast-on technique
Ceramic Firing:
Remarks
1) When veneering with ceramics with higher firing temperature, oxide firing must be carried out at the highest ceramic firing temperature; max. temperature of 950 °C must not be exceeded.
2) Oxide firing: Please follow the instructions of the ceramic manufacturer.
3) Follow the instructions of the ceramic manufacturer.
4) Hardening prior to firing (conditioning for milling techniques): 930 °C, 15min, rapid cooling.
5) When veneered with ceramics, these alloys do not require any additional hardening process to provide their maximum physical values.
6) 25 – 500 °C acc. EN ISO 9693
Solders / Laser Welding Wires:
Remarks
* The working temperature is part of the solder’s name.
** Recommended flux:
Precious metal/ precious metal: use suitable flux
Precious metal/ non precious metal: use suitable flux
Non precious metal/ non precious metal: use suitable flux
1) Herador Lot V800 must be soldered under vacuum. Graphite firing trays should be used.
2) Recommended alternative alloy.
3) When processed with HeraCeram.
5) Accurate temperature control must be ensured. 740 °C must not be exceeded. Maximum heat-rate: 55 °C/min.